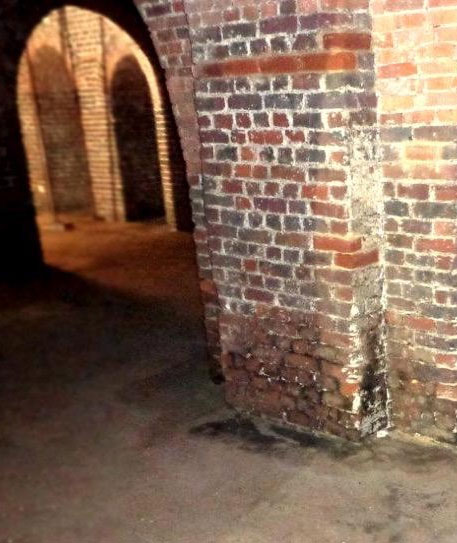
Walls against the ground, like those in most basements and cellars, are in danger of being affected by moisture. To avoid any inconvenience, it is necessary to apply protection:
– From the inside: With the creation of a casing combined with a water-repellent injection
– From the outside: The positioning of a multi-layered protection and the installation of drains along buried walls.
These devices make it possible to very effectively combat moisture in walls.
WHERE
- Inside cellars, walls in lateral contact with the ground.
- Or from the outside, digging a trench along the walls backing onto the ground.
SYMPTOMS
- Damp cellar walls and floors.
- Crumbling of paint or coatings.
- Water infiltration.
- Unpleasant odours, moulds and fungi developing on objects stored there.
- Ambient humidity too high in basements.
WHY DO IT?
Hydrotec provides a 10-year warranty on the protection of buried walls.
INTERIOR PROTECTION: DAMP PROOF CASING / CEMENTING
-
Preparation of the wall to be treated:
-
Stripping of any coating, paint sanding.
-
Filling of cracks.
-
Concrete roughening to ensure good bonding.
-
-
Sawing of a floor and cope tile strip, if necessary.
-
Application of a bonding layer (Hydro+ and Hydrobond).
-
Casing by applying a water-repellent mortar (Hydro+) to a minimum thickness of 14 mm to withstand high water pressure.
-
Installation of Hydro+ mortar chamfers at the foot of the wall and in the corners.
-
In some cases, a drainage channel is placed at the foot of damp walls exposed to high water pressure. This channel will bring the water to a lifting pump installed in a sump.
-
Insertion of an injection barrier to block the rising damp and avoid shifting the damp problem to the top of the wall (if necessary).
-
Lining the floor by applying an”Egaline Hy” or installation of a draining membrane.
-
Possible installation of partitions in the framework of a living room: the casing must not be perforated in any case, a partition will allow the installation of technical ducts without compromising the sealing of the protection.
Particular attention is paid to the passage of pipes at the foot of the wall and to the connections between the floor slab and the wall, as well as in the corners (chamfers providing a reinforced seal).
-
Digging of the trench along the walls to be treated.
-
External cleaning of the damp wall.
-
Injection éventuelle de produit hydrofuge à la base du mur
-
Possible injection of water-repellent product at the base of the wall.
-
Repair of cementing or complete cementing of the unearthed wall (Hydro+ or Hydroseal plaster, depending on the case).
-
Positioning of a rotproof membrane made of polyolefin honeycomb (DELTA MS or PLATON systems) providing vertical sealing. The membrane is terminated at the upper zone by a profile deflecting the water streaming along the wall.
-
Installation of draining mattress (Enkadrain) protecting the membrane against perforation and bringing water directly to the drain.
-
Installation of a drain surrounded by geotextile and gravel.
-
Connection of the drain to the sewer.
For reinforced concrete structures, as a complement to the casing, we use PU resin injections:
When the walls on the ground are reinforced concrete walls (here we are talking about underground car parks, basements of large buildings), the injection of a sealant into the joints in the concrete is a recognized technique for making a wall or soil resistant to water infiltration.
An existing degraded structure can thus be repaired quickly and in a localized manner without risk of damage. This method is ideal for repairing concrete walls or concrete floors with cracks and infiltrations of groundwater.
Where
-
In underground car parks and cellars.
-
Cracked concrete walls or floors.
When
-
Before casing, when treating a damp basement.
Why
-
To avoid having to destroy the existing structure by consolidating it in a sustainable way.
-
The injection of concrete is totally harmless to the occupants in the case of living rooms: we use only products without phthalates or solvents.
How
-
Regular drilling every 25-30 cm.
-
Injection of pressurised water.
-
Single-component polyurethane resin injection, without phthalates or solvents.
-
Installation of a chamfer in vertical and horizontal corners.
-
Creation of a Hydro+ / Hydroseal finishing casing